CONTINUOUS IMPROVEMENT
The continuous improvement model is a mindset – and not a single point in time. It’s an ongoing effort of applying actions over and over in a structured manner in order to improve your business. Continous improvement is a key step in making change happen.
The importance of lean continuous improvement is the level of transformation it has had on manufacturers today. The iterative approach to realising incremental improvements calls for an ever-evolving mindset that drives performance levels higher and higher. Modern manufacturing is a network of interconnected processes that together make up the operational system for producing finished goods. Improving these processes can be complicated because the complexity involved means that a disciplined methodology and sustained effort is required.
Manufacturers embrace the challenge of implementing lean continuous improvement methodologies because these programs deliver a number of benefits. The benefits of lean continuous improvement tools include increased customer loyalty, improved value creation and delivery, consumer expectations regarding product improvements, and survival in today’s global economy.
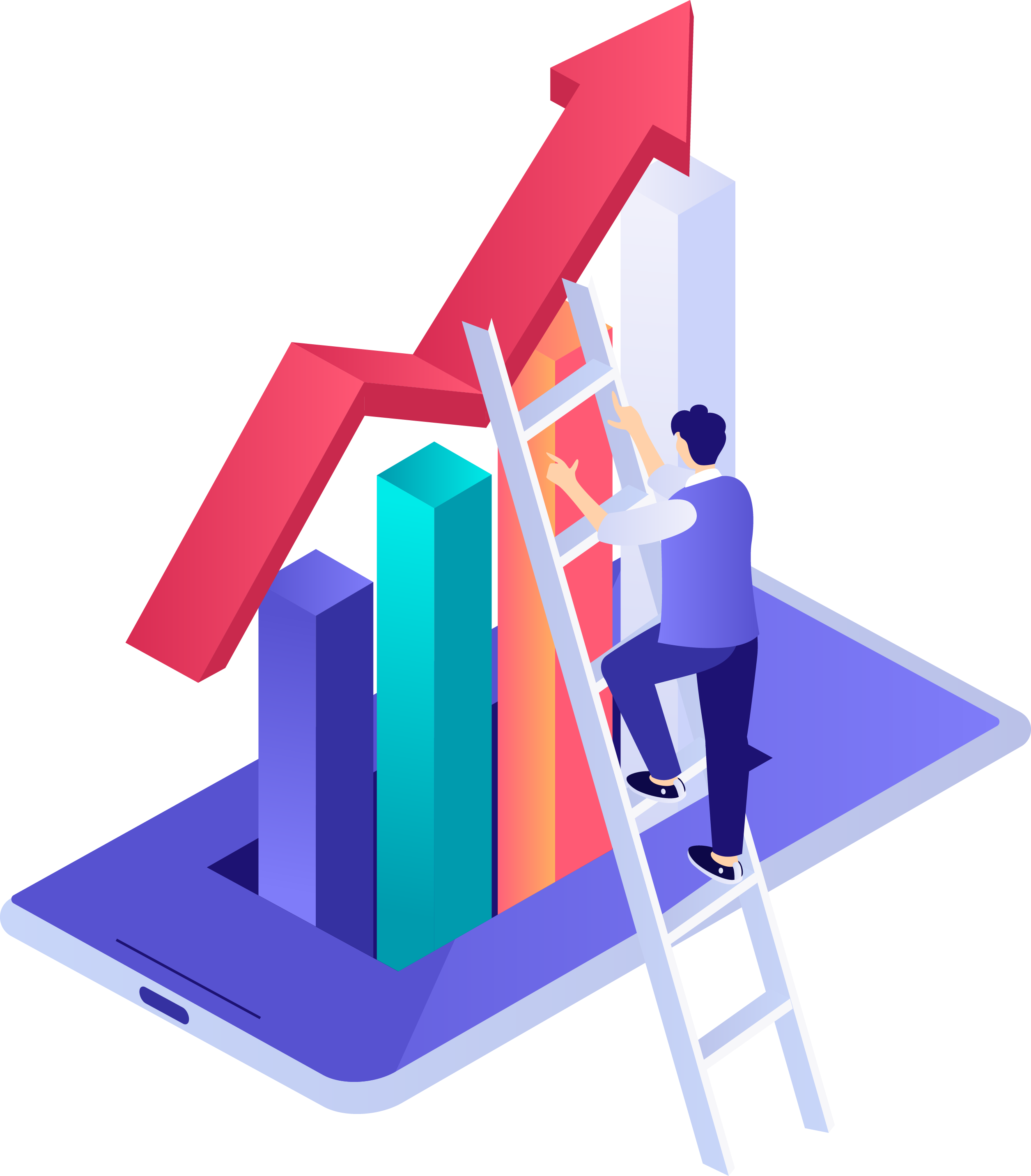
quality criteria
As any business owner knows, the most important component of a organisation is its customers. Your organisation needs to deliver what your customers want and need (even when these are not always clear to the customer).
process improvement
Statistical methods are widely used in business today to track and measure performance. By analysing the data, you can pinpoint the areas that need improvement. Quickly improving areas of weakness is an important part of a continuous improvement model.
the value stream
The value stream is the path that a product takes from its conception to its sale. A value stream map shows where quality issues might arise within the process, allowing them to be addressed through improvement initiatives.
trust & empowerment
Enabling employees to implement and benefit from change is fundamental to continual improvement. Empowering them to identify and implement positive change will likely lead them to enjoy their work, and help build momentum towards a culture of continual improvement.
business process
A business process is not just defined as the steps it takes to complete a single task, but, the activities that result in a specific service or product. Without understanding the processes in place, you can’t be clear on what you are improving.
drive for perfection
A continual drive for improvement is based on a quest for perfection. Perfection is something that can rarely be achieved, but it is necessary to set and achieve new goals that challenge you in order to keep moving forward as a healthy business.