Benefits of Lean Six Sigma: a customer-centric business improvement methodology
Lean Six Sigma is a business management strategy where the core focus is reducing waste and increasing process efficiency to ensure sustainable value for your customer. This method helps your business detect inefficiencies in process and figure out how to best remove them to improve your products and services.
The main goals of Lean Six Sigma implementation are:
1 Provide value to your customers
2 Eliminate waste
3 Continuous improvement
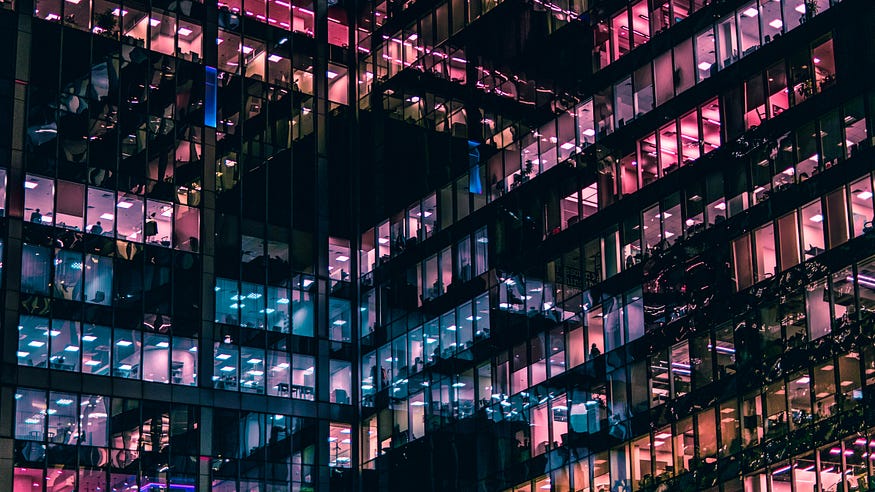
In every industry, businesses are looking for ways to add value, whether reducing lead times in the supply chain, improving the quality of products and services, or reducing wasteful activities that lead to unnecessary costs. This approach helps organisations become more agile and responsive to change.
As Lean consultants continually see such positive results on productivity within businesses, Lean has become a universal management tool and is widely used across all industries including manufacturing, finance, healthcare, IT, military, construction, education, services, and government.
BENEFITS for business
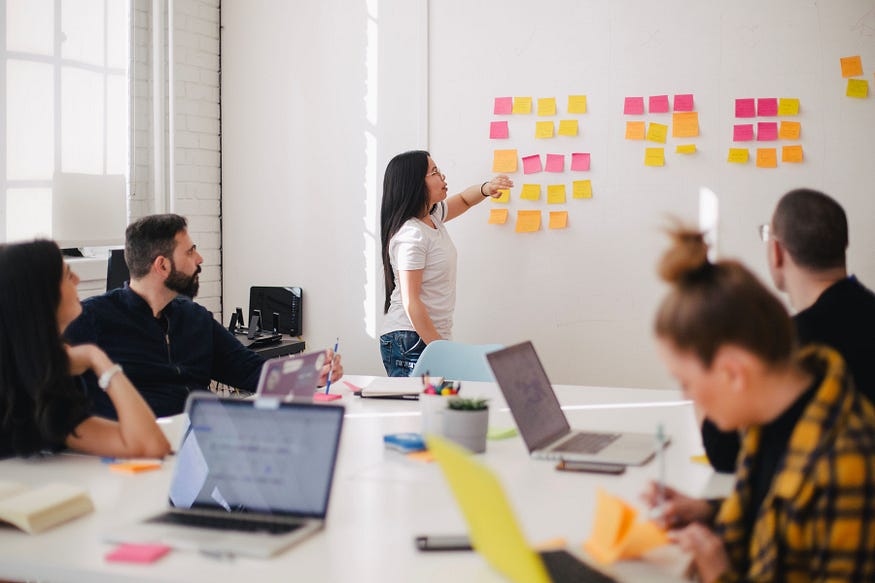
∑ Increased process efficiency. If any steps or processes do not add value to the final product and customer or are found to be otherwise wasteful, they are eliminated or reduced as much as possible, thereby saving time on unnecessary activities.
∑ Increased team engagement. Transparency at all levels of the company promotes respect and a common awareness among employees of the company’s direction, their role in it, and how everyone can contribute to the organisation’s success. Change is never easy, people often resist it, but if you involve employees early in the process, they are more likely to accept it and share ideas to improve the workflow.
∑ Strong customer relationships. The Lean process encourages your company to think in a customer-oriented way and only supports the processes and products that add value for the customer. Creating value for a brand, products, or services is understood through dialogue with your clients. Once your company has achieved this goal, customers will naturally be inclined to come to you for products and services over that of competitors.
∑ Standardized and simplified process. Developing standard techniques that are easy to learn, use, and improve allows your staff to work faster and more efficiently so your business can continue to grow.
∑ Continuous improvement mindset. Implementing an ongoing process improvement strategy into your organisational culture takes time and patience. It’s a strategy that must be adopted by your company, focusing on realising your vision, and working consistently to maintain it. Lean Six Sigma goals are oriented toward the organisation’s long-term success, but however successful or efficient a company is, there is always room for improvement.
∑ Reduced bottlenecks. Through a strategy of continuous improvement, and monitoring, bottlenecks can be seen in advance. Through these methods it is possible to eliminate them at an early stage and ensure operations can run smoothly.
∑ Cost reduction. Implementing Lean principles can lower production costs by increasing productivity, reducing production time, eliminating inventory, and minimizing errors. Sustainable development in businesses is achieved when they adapt to these changes.
Most companies understand Lean methodology as a process of reducing and eliminating waste, but this is not enough to succeed and can still fail if it isn’t done right. The true purpose of Lean management is to transform the culture of the organisation at all levels, from top to bottom.
All employees should understand the company’s vision and work to achieve its goals. Most importantly, Lean is not a short-term solution to a problem but a never-ending, continuous strategy that requires time and patience.
Learn more, access downloadable pdf resources, use our free Process Maturity Assessment Tool or reach out to us directly for a chat on how Lean can help you.