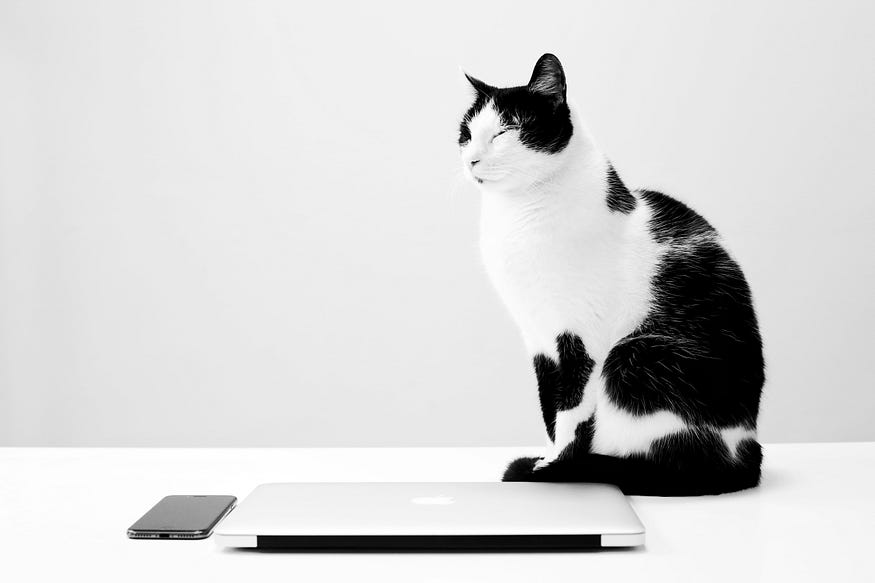
Let’s face it, running a business today isn’t easy. The difference between thriving and just surviving often comes down to how well you can streamline operations and adapt to changes. But how? Enter Lean thinking and a culture of continuous improvement — hallmarks of Lean Sigma (or just “Lean”). Lean’s approaches can give your organisation the edge it needs to succeed.
Here’s a whistlestop tour of five key areas where Lean Sigma can make a difference. We keep it real with some examples and starters for action.
1. Operational Efficiency ⚙️
At its heart, Lean Sigma is all about cutting out waste and ironing out inconsistencies. According to the American Society for Quality (ASQ), companies that use Lean Six Sigma principles typically see a 5–7% drop in operating costs every year. That’s real money you can put back into growing your business.
Example: Toyota’s Lean Legacy
Toyota is the gold standard for Lean. Their Toyota Production System focuses on just-in-time production and eliminating waste, which boosted productivity by 15% and brought defect rates down to under 1%.
2. Customer Satisfaction 😊
Improving your internal processes doesn’t just help your team — it’s great for your customers too. By tackling bottlenecks and smoothing out the customer journey, you can keep your customers happy and loyal. A Bain & Company study found that increasing customer retention rates by just 5% can lead to a 25–95% profit boost.
Key Action: Voice of the Customer (VoC)
Lean Sigma’s VoC tools make it easier to listen to your customers and act on what they say. When you consistently deliver what they want (or even better, exceed their expectations), you’re miles ahead of the competition. Lean Green Belt holders and above are equipped to action this effectively.
3. Agility in Innovation 🚀
We all know the pace of change is relentless. To keep up, you need to be nimble. Lean Sigma’s structured frameworks, like DMAIC (Define, Measure, Analyse, Improve, Control), make innovation manageable and repeatable. According to McKinsey, companies that adopt agile principles, similar to Lean Sigma, are 1.5 times more likely to rank in the top financial performers.
Example: Amazon’s Kaizen Culture
Amazon takes Lean seriously, with its Kaizen events tackling specific challenges across teams. These efforts have sped up delivery times and made their warehouses models of efficiency — proof that small, continuous improvements can add up to big wins.
4. Employee Engagement 🤝
More than a cold efficiency exercise, Lean Sigma at its best is an empowering human-aware approach that puts problem-solving in everyone’s hands. This not only makes your processes better but also keeps your employees engaged and motivated. Gallup says that highly engaged teams are 21% more profitable. That’s a win-win.
Empowerment Example: GE Aviation
GE Aviation brings cross-functional teams together to find and fix inefficiencies. The result? A 30% reduction in production cycle times and a workforce that’s energised by playing a key role in the company’s success.
5. Risk Management 🔍
Lean Sigma’s data-driven approach is a game changer for risk management. By identifying potential problems before they happen, you can avoid costly mistakes and ensure compliance. PwC found that companies using data to guide decisions are three times more likely to improve their processes.
Key Action: Failure Mode and Effects Analysis (FMEA)
FMEA is like a crystal ball for your business. Lean Green Belt holders and above are versed in using this to help you pinpoint weak spots and put safeguards in place before things go wrong, saving you headaches and money.
Final Example: 3Ms Lean Transformation
3M is a great example of what Lean Sigma can do. By adopting Lean principles, they cut manufacturing cycle times by 25% and saved over $1 billion in just five years. Their commitment to continuous improvement empowered employees to innovate, ensuring they stayed ahead of the curve.
How to Harness the Power of Lean Internally
Want to make Lean work for your team? Check out Change Consulting Scotland’s Lean Academy. We offer a mix of online study, expert coaching, and super-fast customer support (trainees hear back within 24 hours!). Our approach makes it easy for leaders to embed Lean thinking into their organisations across any and all departments — and see real results.
Final Thoughts
Lean Sigma isn’t just a bunch of buzzwords — it’s a way of thinking and taking action that can transform your business. By enhancing efficiency, customer satisfaction, innovation, employee engagement, and risk management, you can build a company that’s not just surviving but thriving. And as 3M’s success shows, it’s not just about cutting costs — it’s about creating a culture of resilience and adaptability.
Ready to take the plunge and see what Lean Sigma can do for you? Click here to discover your journey — there’s no time like the present!